What Are Transfer Dies?
Transfer dies are a modern solution in the world of metal stamping, used predominantly in high-volume production environments. Unlike progressive dies that keep the workpiece attached to a carrier strip, transfer dies allow each part to move independently from one station to another within a single press. This process is ideal for manufacturing large, complex, or deep-drawn components.
Each die station is spaced at a consistent interval — known as the pitch — which defines how far a part must travel between forming operations. The entire system is synchronized within a single press stroke, enabling multiple forming stages in a streamlined cycle.
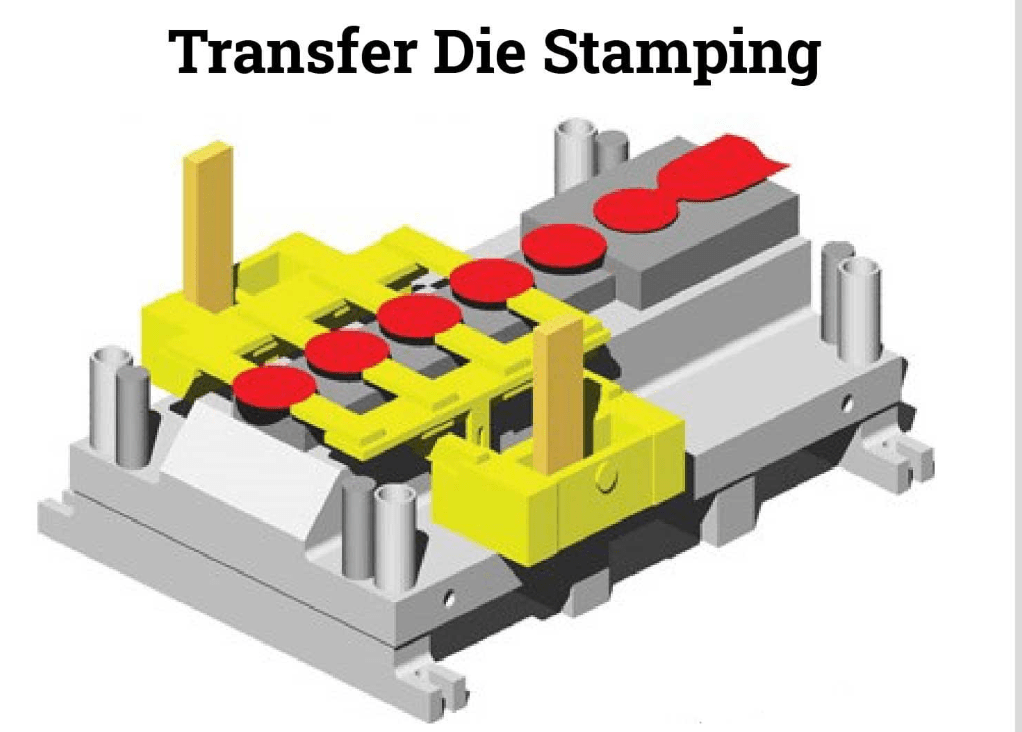
How Do Transfer Systems Work?
Instead of a traditional conveyor or hand-feeding, transfer systems use integrated mechanical rails positioned inside the press to pick and place parts. These transfer rails operate using two main configurations:
1
2-Axis Transfer Systems (X-Y Movement)
These rails grip the workpiece, move it forward to the next station, and release it — perfect for less complex parts.
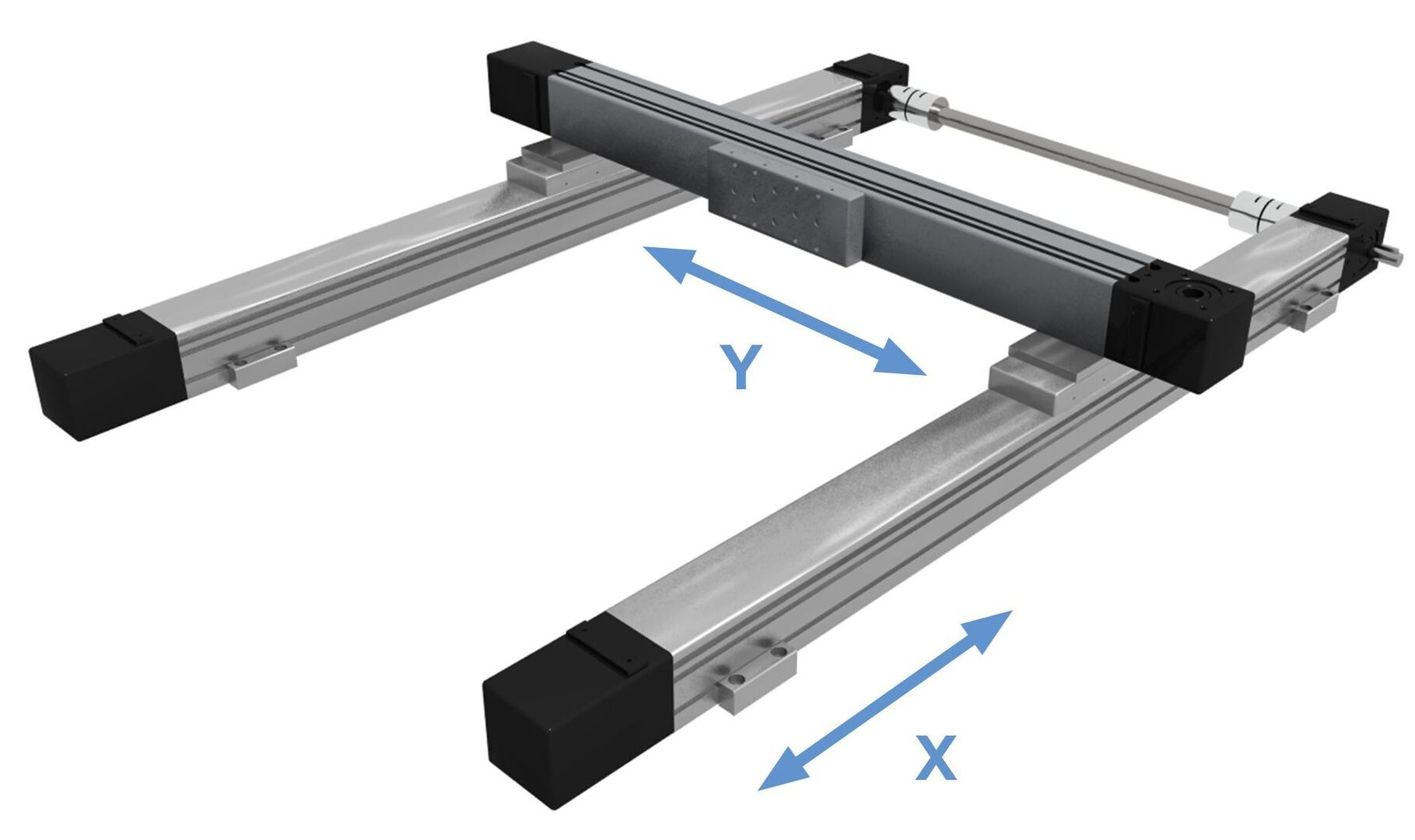
2
3-Axis Transfer Systems (X-Y-Z Movement)
In more advanced setups, rails not only move forward and grip the part, but also lift and lower it vertically, placing it precisely within the next die. This Z-axis motion ensures greater control, especially for deep-drawn or geometrically sensitive components.
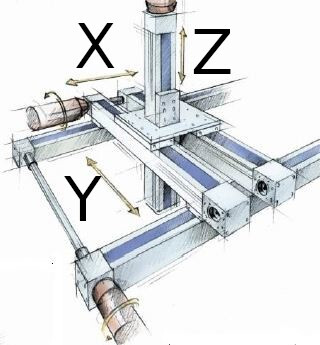
Why Choose Transfer Dies?
Transfer dies are ideal for producing:
Axially symmetrical parts (e.g., automotive hubs, cookware, filters)
Large, deep-drawn components requiring multiple forming actions
Parts with features on multiple planes or requiring part orientation changes
Advantages of Transfer Die Systems
Versatility for Complex Parts
Transfer dies accommodate parts that need forming, drawing, trimming, piercing, and flanging — all within a single cycle.
Cost-Efficient Material Use
Since parts are not tethered to a strip, raw material can be cut into blanks in a way that reduces scrap, improving overall material utilization.
Speed Meets Size
Large-sized stampings can be moved efficiently between stations, even at high production speeds.
Programmable Servo Transfers
Modern transfer rails are driven by servo motors, allowing for precise synchronization with press speed, stroke length, and part geometry.
Part Reorientation Capability
The system allows in-cycle part flipping or rotation, essential for complex geometry components.
Where Ahlu Engineers Adds Value?
At Ahlu Engineers, we specialize in designing and building precision-engineered transfer dies tailored to your application. Our in-house expertise allows us to:
Customize die pitch and station layout for optimal throughput
Integrate servo-driven rail systems to enhance speed and flexibility
Engineer dies that handle complex, large, or deep-drawn parts with minimal operator intervention
Provide end-to-end die validation and try-out support
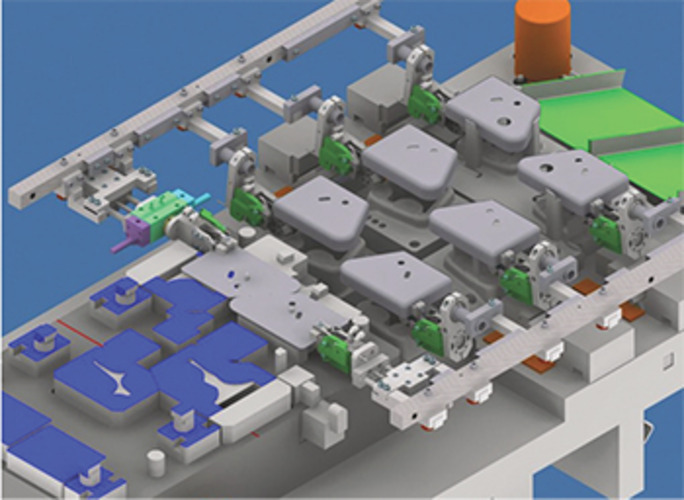
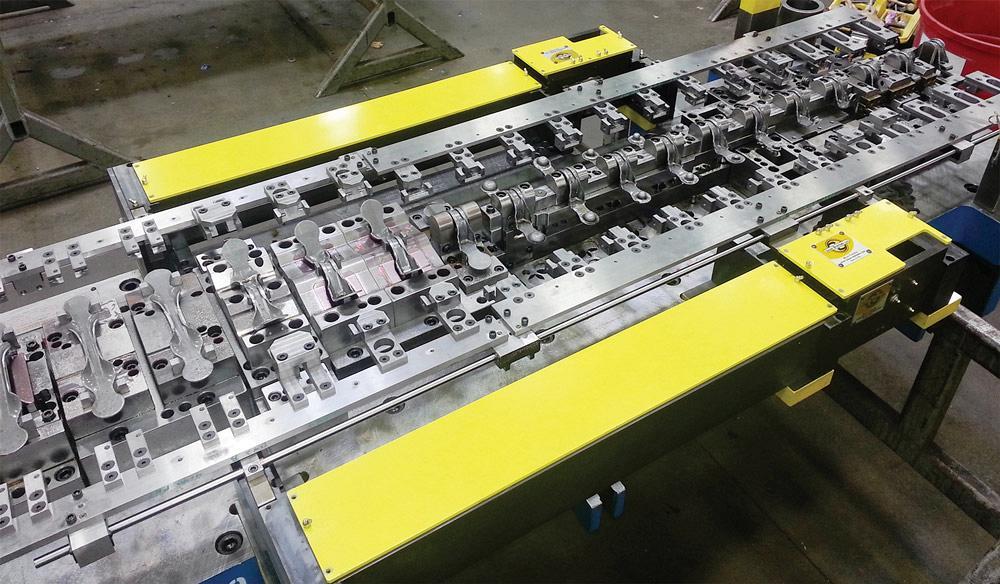
Industries We Serve
Automotive
(Chassis, Brackets, Suspension)
Consumer Appliances
(Cookware, Fan Covers)
Electrical Enclosures
Industrial Components
HVAC & Plumbing
Need Transfer Dies That Work Smarter?
At Ahlu Engineers, we don't just build tools — we engineer solutions that upgrade your production floor into a high-efficiency, low-waste environment. Contact us today for custom transfer die development, press automation consultation, or complete tool design services.
Explore Our Premium Solutions
Our wide array of expertly designed automation solutions, tailored to enhance your manufacturing processes with precision and efficiency.
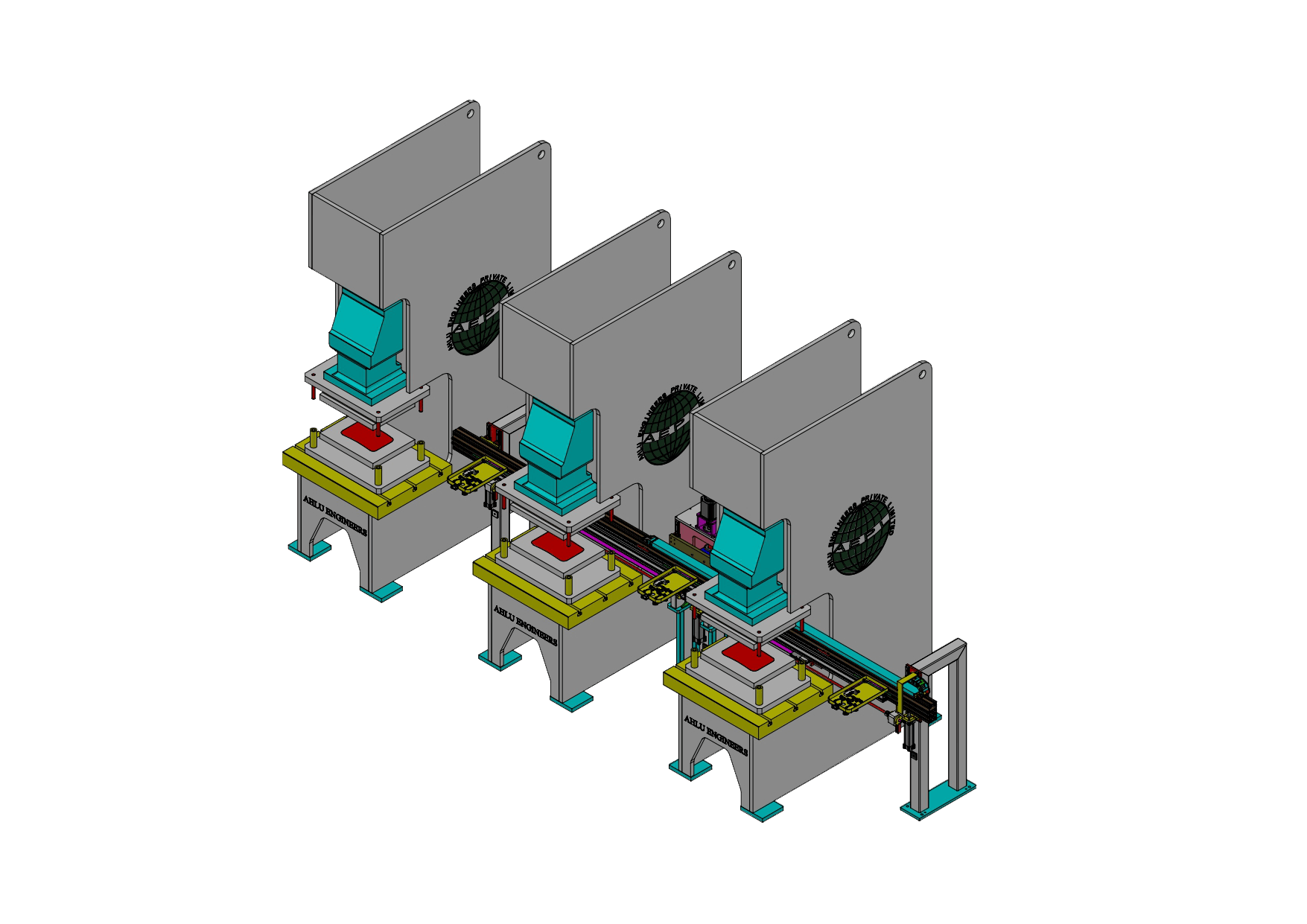
Ahlu Multi Press Transfer System- AMPTS Series
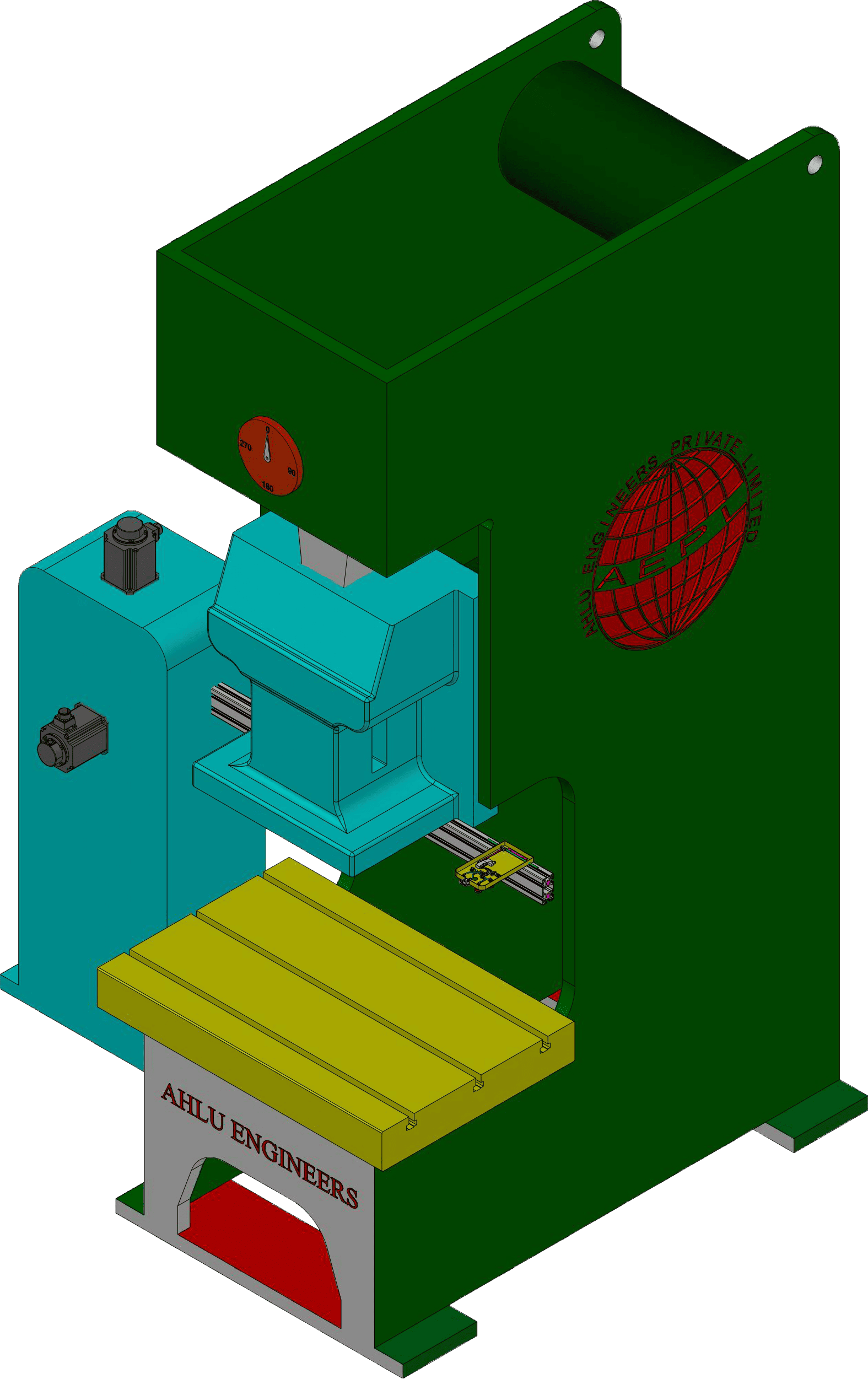
Ahlu Cantilever Servo Transfer System- ACSTS Series
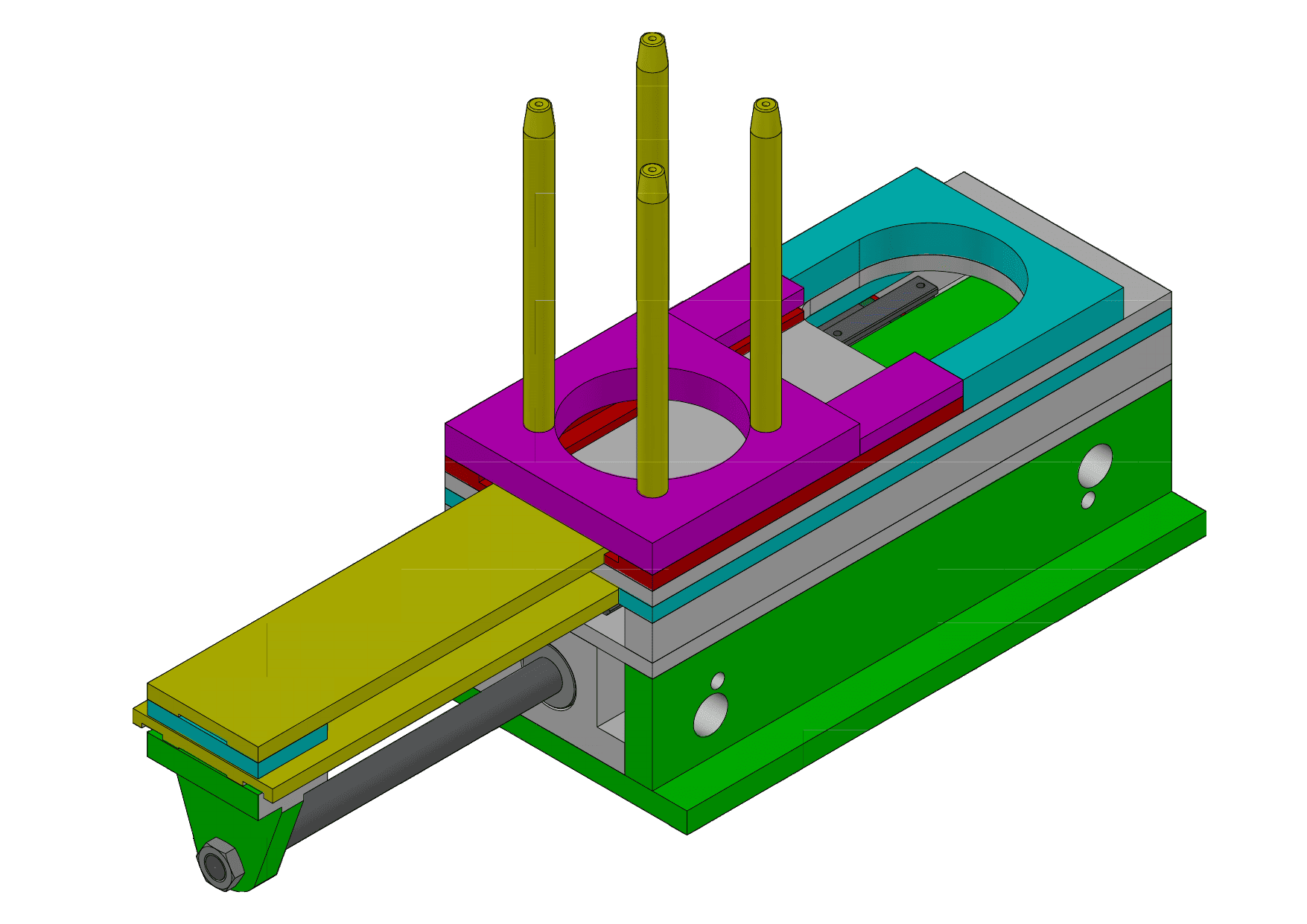
Ahlu Blank Feeder- ABF Series
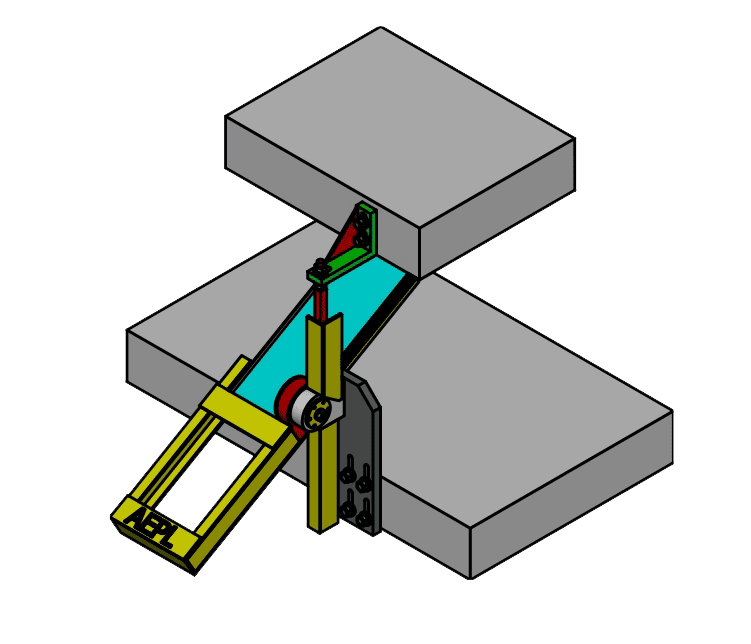
Ahlu Mechanical Press Flap Series- AMPF
Need a Custom Automation Solution?
Our experienced engineers specialize in designing tailored automation systems that perfectly match your unique manufacturing requirements. From concept to implementation, we deliver precision-engineered solutions that boost productivity and efficiency.
✓Expert Engineering Team
45+ years of automation experience
✓Industry Leading Innovation
Cutting Edge automation solutions for modern challenges
✓Complete Support
From design to maintenance & training
Our automation experts are here to help.